Изготовление матрицы из стеклопластика, Изготовление матриц

Обычно они достаточно заметны и редко удаляются. При шпаклевке и окраске лаком необходимо использовать материалы, которые достаточно хорошо выдерживают воздействие стирола. Применение стеклопластика в промышленности — приоритетный выбор многих современных организаций. Использование восковых пластин требует умения и навыков для достижения наружного результата.
Когда речь идет о тонкостенных матрицах, чтобы не возникало напряжений натяжения, усиления и рамы следует приформовывать следующим образом:. Необходимо обозначить места установки усилений. Поверх меток приклеивается липкая лента, выдерживающая воздействие стирола. Приформовываются два слоя стеклоткани сатинового плетения поверх пленки и устанавливаются сердцевины усилений, картонные трубки, полиуретановые лоскутки или соответствующие элементы поверх стеклоткани. Приформовывается усиление и дается время на отвердение.
После отвердевания весь пакет отделяют и удаляют пленку. Очень хорошо получаются широколапые балки усиления. Далее необходимо отшлифовать на матрице поверхность и приклеить усиление на поверхность одним или двумя слоями стеклоткани сатинового плетения.
Для сведения к минимуму риска возникновения напряжений натяжения необходимо устанавливать полностью готовые рамы, сделанные из металлического уголка, стальной трубки и пр.
Когда рама приформована к матрице, ее поверхность уже нельзя обрабатывать: шлифовать, полировать или сверлить. Различные части рамы необходимо обработать отрезать, сгибать так, чтобы они полностью подходили к матрице. Каждую часть временно приставляют к матрице до полного прилегания и соединяют вместе держателями, струбцинами и пр.
В крайнем случае, различные части соединяют, точнее, прихватывают точечной сваркой. Когда рама готова и временно собрана, ее снимают с поверхности матрицы и сваривают целиком. Высверливают все отверстия и устанавливают все элементы, необходимые при работе с матрицей. После этого всю раму полностью очищают от жира и устанавливают обратно на поверхность матрицы для приформовки.
Необходимо помнить, что у приформовываемых к матрице частей, должно быть стопроцентное прилегание. Все зазоры должны быть заполнены шпаклевкой до приформовки. Если прилегание полное и приформовываемые поверхности отшлифованы, достаточно двух слоев стеклоткани сатинового плетения и широких крепежных лопастей речь идет о ширине приформовочного угольника приформовки.
При формовании необходимо помнить о тепловом расширении рамы. Крепление рамы и стойки. Раму необходимо спроектировать так, чтобы она была местом крепления стойки и прочих необходимых для обработки матрицы деталей. Рама не должна быть только лишь кучей металла, а у каждой части должно быть собственное предназначение и определенное место.
Разделение матрицы необходимо осуществлять вдоль естественных линий раздела так, чтобы раздел следовал углу или аналогичному элементу. Разделяемые части необходимо снабдить вытяжными ручками для облегчения открытия матрицы.
Разделяемые матрицы, в которых линия раздела не должна просматриваться на изделии, необходимо изготавливать особенно тщательно. При обработке больших матриц это весьма трудоемкий процесс.
Во многих случаях приходится шпаклевать или шлифовать выделяющиеся линии раздела. Если большие половины матрицы перекрываются внахлест, то можно избежать шпаклевки, изготавливая т. Этот формовочный край можно шлифовать и полировать в дальнейшем и таким образом, можно избежать больших ошибок при стыковке частей матриц. Разделительные крылья, замковые края не следует делать ровноповерхностными.

Их недостатком является то, что закрывающая сила, которая держит части вместе, разделяется на две большие области и часто немного на сам разделительный край в котором нужна была бы значительно большая сила. Разделительные крылья нужно отформовывать так, чтобы сила сжатия была направлена непосредственно на саму разделительную линию или вблизи ее, насколько возможно.
Формование разделительного крыла для достижения оптимальной возможной силы запирания. Разделяемые матрицы изготавливают следующим образом. На разделительную линию устанавливают временный фланец, после чего матрицу собирают в две стадии.
Временный разделительный фланец необходимо натереть воском и обработать разделительным материалом так же, как и болван. Когда будет полностью изготовлена отформована и отверждена оболочка первой половинки матрицы, то можно снять временный фланец крыло.
Поверхность раздела готовой половинки матрицы после этого необходимо натереть воском и обработать разделительным материалом. Обработку необходимо производить аккуратно и осторожно, чтобы не отделить от болвана готовую половинку матрицы. Формуя второй фланец, надо дать стеклоткани завернуться через край так, чтобы фланцы приклеились друг к другу снаружи. Это делается для того, чтобы фланцы не сломались и не разошлись бы до окончания формования.
Разделительные фланцы необходимо сделать достаточно жесткими, чтобы их форма несмотря на силу сжатия, сохранялась при использовании матрицы. Направляющие являются неизбежными деталями в разделяемых матрицах. Их главное значение - не направлять части матрицы, а удерживать их эти части на правильных местах. В больших матрицах длинные направляющие, которые требуют одноосного перемещения частей матрицы, являются не практичными.
Если направляющим придать конусообразную форму, то матрицу можно будет запирать и открывать также в диагональном направлении. В матрицы, у которых края изготавливаемых частей подрезаются до окончательного затвердевания, можно заформовать стальные края.
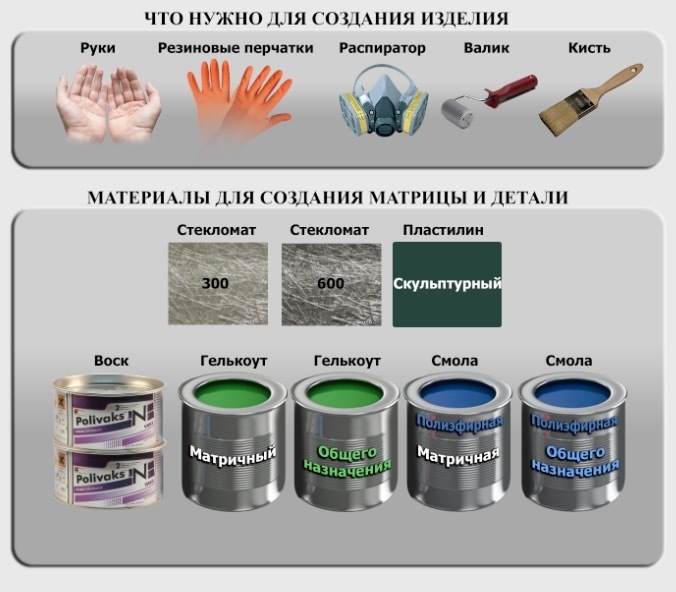
Обрезные кромки стоит делать с самого начала. Если поверхность изделия находится вдоль одной прямой, то соответствующие стальные кромки можно сделать линиями раздела в разделяемой матрице. В изгибающихся линиях раздела это не очень пригодно, поскольку существует опасность, что касание будет не полным.
Как уже упоминалось ранее, поломка стеклопластиковых матриц чаще всего происходит из-за грубого обращения.
Особенно частой ошибкой является применение силы и острого инструмента. Это обстоятельство необходимо принимать во внимание уже на стадии проектирования и изготовлять, например, задние углы, разделительные уровни и пр. Таким образом, необходимо обеспечить, чтобы отделение изготовленной детали от поверхности матрицы было бы легким. Съемник - это деталь, значением которой часто пренебрегают. Правильно расположенный и хорошо изготовленный съемник значительно увеличивает долговечность матрицы.
Ее можно изготовить различными способами. Самый простой - отверстие против точки нажима, которое на время формования закрывают липкой лентой, винтом или вытяжным штырем. Это простые и дешевые способы. Однако, при изготовлении больших и тяжелых деталей у них к сожалению проявляются недостатки.
Съемник не должен поднимать или вытаскивать деталь наверх, а должен пропустить воздух между деталью и матрицей, чтобы они отделились.
Хороший съемник получается, когда он изготовлен в соответствии с рисунком в виде трубчатого вентиля. Он работает так, что открывается на десятые доли миллиметра, вследствие чего воздух попадает между поверхностями, отделяя деталь от матрицы.
Такой съемник можно использовать также в вакуумно-инжекторных матрицах, когда к трехканальному крану подключают пневморукав так, чтобы съемник-выталкиватель находился в таком же разряжении, что и внутренняя часть матрицы.
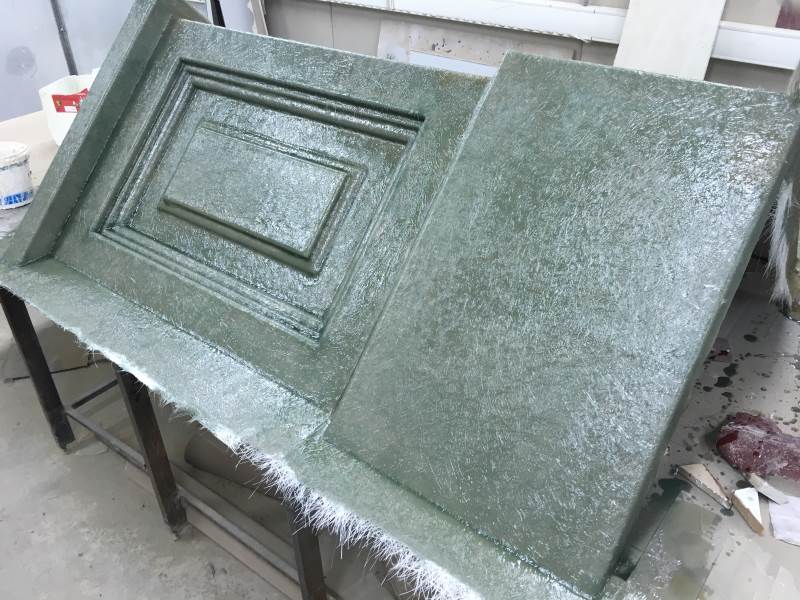
Съемник необходимо устанавливать в центр матрицы, в ее самое глубокое место, не слишком близко к раю. При необходимости отделения больших или толстостенных деталей, съемник устанавливают ближе к тому краю, где отделение произойдет легче. Если деталь глубокая и у нее маленькие задние углы, то съемник устанавливают также и на края. Если съемник расположен на боковой поверхности матрицы, необходимо помнить, что доступ воздуха надо прекратить сразу после отделения, чтобы отделение происходило при закрытом съемнике, иначе деталь может поцарапаться сама или повредить съемник.
Необходимо дать матрице пробыть на поверхности болвана в теплом помещении и дать ей отвердеть достаточное количество времени, не меньше трех недель. Имея достаточно времени на изготовление матрицы в дальнейшем можно избежать многих неприятностей.
Тогда, когда поверхность болвана не подвергается воздействию стирола, и тщательно сделано воскование при отделении от матрицы не возникает проблем. При нагнетании воздуха в съемники, матрица легко отделяется и ее можно поднять.
Если против всех ожиданий матрица не отделяется от болвана, не следует применять силу, а стоит попробовать следующие методы:. Если никакой из этих способов не помогает - потянуть блоком или домкратом или вырубить болван аккуратно кусок за куском.
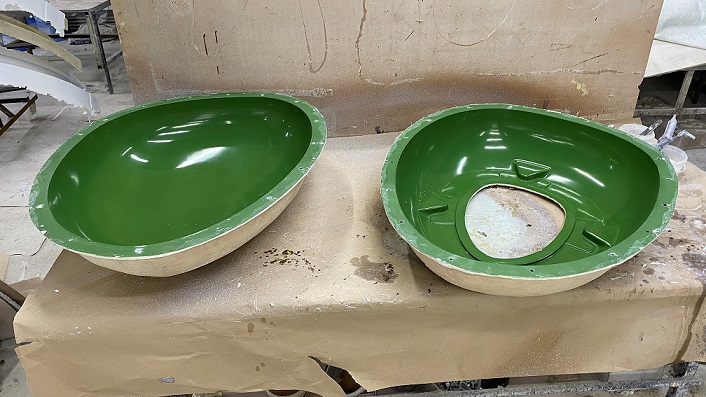
В действительности этот метод повреждает также и матрицу. Матрицу необходимо вымыть прохладной водой и моющим веществом для посуды либо мыльной водой. Необходимо проверить поверхность, направляющие и необходимое для обработки матрицы оборудование, а также проверить съемники и замковый механизм. Если на поверхности матрицы имеются возвышения или отсутствует блеск, то необходимо выполнить водную полировку.
После водной полировки поверхность надо отполировать с помощью системы Profile Standart от Farecla. Сначала следует использовать пасту Profile , а затем последовательно эмульсии Profile и Profile Если поверхность только лишь матовая тусклая , без прочих дефектов, полировки полирующими веществами может оказаться достаточно для доработки.
Когда качество поверхности матрицы проверено и отрегулированы все дополнительные механизмы: съемники, выталкиватели и пр. Это воскование выполняется таким же образом, как и воскование болвана. После воскования на поверхность наносится разделительная пленка и осуществляется вручную пробное формование. Пробное формование необходимо выполнить с декоративным слоем и 4-мя слоями стекломата мокрый слой против мокрого. Пробное формование необходимо сделать также инструментам сжатия, матрицам из ячеистого пластика и на обе половинки двухсторонних матриц.
Таким образом проверяют также отверждение поверхности матрицы. После пробного формования поверхность матрицы надо вымыть прохладной водой и натереть еще раз Hi-Low. После этого наносят разделительную пленку и матрицу подготавливают для изготовления первой детали. Перед первой деталью часто имеет смысл выполнить еще одно ручное формование в матрице. Это формование необходимо сделать также аккуратно и с той же техникой, что и формование наружной оболочки. Эта тщательно изготовленная деталь становится тогда "архивной копией" контрольное фальшизделие и ее можно использовать в качестве болвана для дополнительных матриц.
Когда требуется большая точность линейных размеров, эту архивную копию изготавливают с применением эпоксидного связующего. После первой детали или "архивной копии" матрицу необходимо снова вымыть и натереть воском.
Также и для третьего формования необходимо использовать разделительную пленку. Начиная с четвертого формования пленку можно не наносить, а восковать каждый второй раз. Когда будет изготовлено около 10 деталей, можно прекратить воскование через раз и изготавливать после каждого воскования детали небольшой серией изделий. Проблемой изготовления рабочей оснастки для стеклопластикового производства является усадка полиэфирной смолы.
Эти оценки относятся к ненаполненной полиэфирной смоле. Наполненная полиэфирная смола усаживается меньше, поскольку часть от объема составляет не усаживающийся материал.
Это идеальные теоретические оценки. На практике усадка изменяется очень значительно в зависимости от многих факторов, которые влияют на полимеризацию во время изготовления. Усадка следует за процессом отверждения, так как оно отверждение начинается при коагуляции смолы и продолжается до тех пор, пока не произойдет окончательная полимеризация.
Если у усадки есть физическое препятствие в каком-нибудь направлении, в этом направлении со временем могут развиться внутренние напряжения. Если препятствие для усадки удаляют прежде выравнивания напряжения, это может привести к долговременному усадочному напряжению, так как эти напряжения требуют длительного времени для выравнивания.
Это явление вызывает изгиб стеклопластиковых изделий, и смолосодержащие места - скопления в углах декоративного слоя, подтеки - растрескиваются. В данном случае переднего бампера. Перед снятием матрицы изделие, с которого будет сниматься матрица, обрабатывается специальным разделительным воском. Несколько раз наносится и располировывается, чтобы создать микроразделительный слой. Это поможем в будущем с легкостью достать изделия из готовой матрицы. Воскование также придает глянцевый эффект.
По-хорошему слоев нужно, дня уходит на воскование. Далее делаются так называемые фланцы. Это обортовка матрицы. Малейшая ошибка или недочет, и будущее синтетическое изделие можно смело выбрасывать. Естественно, такого происходить не должно, и современное оборудование, используемое специалистами нашей фирмы, это позволяет.
Наша компания предлагает своим клиентам уникальную возможность. Мы давно и успешно работает с таким материалом, как стеклопластик, а новейшая технология 3D фрезерования позволяет нам быстро, точно и качественно проводить изготовление матрицы для стеклопластика.
В зависимости от пожеланий заказчика наши специалисты также могут создать матрицу оснастку из МДФ, углепластика и алюминия. Принципиально конструкции всех стеклопластиковых матриц одинаковы, при этом неважно, для чего будет применяться полученная оснастка, разница может быть только в сырье, и незначительной специфике того или иного варианта. Но общие требования остаются неизменными — изготовление стеклопластиковой матрицы должно производиться с таким расчетом, чтобы конечное изделие отличалось:.
Наша компания создает матрицы с применением самых последних технологий, она обрабатывается высокоточными инструментами, а само изготовление стеклопластиковой матрицы состоит из формирования двух слоев — верхнего, декоративного и внутренней отливки или каркаса.
Декоративный слой придает изделию форму, а внутренний наделяет высокой степенью прочности и жесткости. Помимо высокого качества исполнения и приемлемой стоимости работ мы предлагаем нашим клиентам выбрать наиболее удобный вариант взаимодействия.
Изготовление стеклопластиковой матрицы нашими специалистами может производиться как по эскизам заказчика, так и по собственному дизайн-проекту, созданному на основании требований последнего.